Wood coatings
Wood Coatings
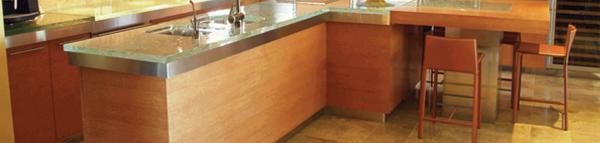
Natural, Artificial, Synthetic this is the world of wood coatings. Let us have a glance.
• Natural coating
Veneer
Veneer is the thin layer of natural wood which however has the number of disadvantages. Different color, cracks and knots of the same wood species make impossible to form the solid sheets depends on the thickness of the most wood species. The newest "fine line" technology allows avoiding all these disadvantages without making the veneer artificial. The basic features of this material are stable veneer’s color and texture from batch to batch, absence of minor defects, and possibility to obtain large sheet needed for door leaf manufacturing. The sheet size allows to finish the door leaf without sticking together separate strings and to avoid the risk of fractures or careless joints.
Veneer is applied to chipboard or an MDF base. A natural timber veneer can be applied to both sides. This is sealed with a clear coating of oil for durability. The color range is limited to the availability of the timber species, any additional color shades are stained in one of thousands of options.
Edges of veneer boards are square and in the same material, on wide boards a matching veneer strip is placed side-by-side, so a tiny join could be showing. Veneer is usually only applied to flat panel doors with square or beveled edges, as bending of veneers is limited.
As wood is a natural product, it should not be exposed to air that is too humid or too dry. For a kitchen with wooden doors air humidity of 40 to 85% is ideal, dry air with little to no humidity is undesirable.
• Artificial Coating
Artificial coatings are composite materials made of single sheet or layer of papers (decorative or non-decorative) that can be treated with resins such as melamine formaldehyde and phenol formaldehyde.
These sheets may coated by different resistant cover sheets such as (acrylic, PVC, etc.) are used on MDF and chipboard. There are several wood substitutes which we try to list here.
Foil and Vinyl
What are Foils and Vinyls?
These are increasingly popular wood substitutes that give a very realistic wood grain finish to MDF and chipboard. The particular benefits are economy, an extensive range of imitation, exotic wood effects, durability, and consistency of color and grain that make them ideal for fitted furniture, without the open graining and blemishes.
Foil
Foils are photographic reproductions of timber, used in place of real wood veneers on MDF panels and available in a variant kitchen or bedroom cabinet doors, plinths, pilasters and cornices. Foil doors are normally constructed as "five piece" doors to imitate traditional timber doors.
Vinyl
Vinyls are economically priced, wood grained, flexible plastic surfaces that mould themselves to and bond to "one piece" pre-shaped MDF doors, in approximately 30 designs and 35 colors.
Vinyl wrapped doors are made up of MDF panels which are cut, routed, profiled, sanded, then glued and covered with a vinyl film that is pressed to the door under vacuum. The back of the door is usually pre-laminated. The vinyl thickness is between 0.4mm and 0.7mm.
There is a large range of colors, both plain and in wood grain, sometimes they are embossed to feel like wood grain or textured for effect. Some vinyls are available with a shiny gloss finish. Colored gloss vinyl is the cheapest material used for gloss finish doors.
The edging on vinyl is better than laminates, as it is more rounded, without sharp corners, and has no joints.
Acrylic coatings
The second types of the thermoplastic coatings are acrylic sheets. These coatings contain all PVC coatings advantages including shaping and high flexibility in temperature 70 to 80 ° C in membrane press besides having impact resistance, and unique capability of restore. In a way that all damaged surfaces could be repaired and restored to all levels that not easily detectable.
Furthermore, the sensitivity of this type is less than PVC against the light of cigarette and sunlight. It should be mentioned that his coat covers the great variety of colors. It can be used to cover on the surface of the craft compound door, furniture, cabinet and sound box, also can cover veneer and thermal transfer on the surface of the door panel and furniture with the silicon membrane. It is intended for laminate doors, kitchen and furniture facades, different furniture units with PVC films and veneer, with the help of heat and vacuum technique system.
MFC
Melamine faced Chipboard, or MFC is a common product that is made from resin coated particles of softwood. Though it is denser than conventional wood, it is the lightest and weakest type of fiberboard, except for insulation board. The particles are evenly spread over a flat plate and heat bonded together under high pressure. The melamine face refers to the decorative finish found either side of the board, often seen in white but also available in hundreds of colors and wood grains in different textures and sheen levels from matt to gloss.
There are other types of available chipboard including flooring grade, moisture resistant, melamine veneered and plastic veneered (used on worktops). White melamine MDF as well as other colors including of wood grains are favorable on kitchen cabinets, and real wood veneered on cabinet doors.
General application: bathroom, counter tops, kitchen doors, shelving, shop fitting.
Routine cleaning simply involves wiping with a clean, damp, soft cloth. Never use abrasive cleaners, scourer pads like wire – copper cleaning pads, or sandpaper, or subject to excessive wetting.
HPL
HPL is wood fiber with several layers of core, or “Kraft” paper (similar to that used for brown paper bags), topped with a solid color or printed decorative layer and a protective wear layer.
Practical, durable and versatile Color board Low Pressure Melamine Panels (LPM)
Hard wearing, scratch resistant surfaces are the prominent properties of HPL.
The most important proper of HPL is using for post forming of countertops and end panels contemporary and durable surfaces manufactured from post formable high pressure laminate (HPL), affordable and easy to maintain. Protect surfaces longer due to high resistance to moisture. Scratching, UV rays, steam, stains and impacts. Ideal for every day living.
• Synthetic Wood Finishes
(Sealers) or synthetic wood finishes become more popular each year. They can be as easy to apply as an oil finish and they have almost the same durability as a varnish, yet can be somewhat simpler to refinish if necessary.
They are an easy-to-apply alternative that offers good durability and a good-looking finish that offers a different (slightly cloudy) appearance than either varnish or oil.
These are available as tinted or clear finishes. These finishes require basic initial surface preparation, and application is essentially the same as the first coat of a varnish. After that first coat, multiple coats can be applied easily with no surface preparation.
Maintenance costs are much simpler than varnish (hence the appeal!), generally requiring only a cleaning of the existing finish and re-application of a new coat of finish. If there are damaged spots, the technique generally used is a touch up of the damaged area, then an application of finish to the whole piece.
Examples of synthetic wood finishes are including:
Surface Preparation
Different woods will require variations on proper surface preparation prior to the application of the finish. That said basic preparation includes getting the surface smooth and clean to allow for a pleasant looking base, but also to allow the finish to adhere properly to the wood.
This usually includes:
- removing the existing finish
- Bleaching faded or oxidized wood
- Removing natural oils from woods such as teak (alcohol or acetone may be used but, beware the extremely toxic nature of the latter)
- sanding the surface as desired ( sanding raises wood grain, application of a sealer or thinned product when applying varnishes would be a good idea requiring a sanding again prior to application of further coats.)
Oils
Wood or teak oils will penetrate more deeply into the wood fibers and maintain the original look of the wood better than other finishes that are simply surface coatings, but oil has a shorter lifespan than varnish or synthetic finishes.
Oils range in color from clear to dark brown. As with any wood finish, multiple coats will result in a more uniform finish and greater longevity. Oil is usually the easiest to apply but as with any wood finish, it requires some basic preparation for the best results. Clean, sanded teak with several coats of oil can provide 3-6 months of protection. There are several varieties of wood and teak oils to choose from all seem to provide satisfactory results within the 3 to 6 month lifetime of this product.
Varnish
Varnishes have long been the traditional clear wood protector. They are generally made up of oil, solvents, resins, dryers, thinners, and other additives. By varying these ingredients, and by adding UV inhibitors and other proprietary ingredients each manufacturer's varnish will have different characteristics.
Although in many respects they may all quite similar. Varnishes can have a gloss or a satin appearance. They can be extremely hard and durable, and can vary in color from clear to dark amber. One very good idea is to cut the varnish for the first coat on bare wood by as much as 50% with the recommended thinner. This may sound a bit overboard, but it actually allows that first coat to penetrate deep into the wood's grain, allowing for an exceptional bond between the wood and subsequent coatings of varnish. Varnishes generally require at least 6 coats…10 coats is not uncommon. Satin finishes are usually applied only for the last coat on exterior surfaces.
Painted finish
A good finish applied to the wood will provide a barrier to protect against the elements that will attack the wood during the season rain, wind and sunlight. Deciding which to use is often confusing frequently, appearance plays a big part in deciding what to apply.
Hardwood Maple or Birch is used for all Painted styles. Paint will develop hairline cracks in the finish, most notable around the joints especially miter joints. This is a result of natural expansion and contraction of the wood with that, kitchen resource direct uses MDF for center panels with all painted door styles to help with the stability of the door. Painted doors do require more maintenance for chips, marks, residue from normal kitchen use, and hand/finger prints. Paint may also have a slight difference in tones between doors, drawer fronts and face frames.
Glaze Finish
Glazes are hand-applied. Glazing is most apparent in contours where "hang-up" can occur. Doors with less detailed profiles will show less hang-up which accentuates the grain's natural attributes. Glaze adds depth, dimension and an understated appearance that's guaranteed to endure.
-Glazing will range from a consistent, even appearance to varied almost uneven coverage.
-Glaze marks may appear outside of the general "hang-up" area.
-You should expect subtle to dramatic look based on the complexity of a cabinet door's design, as glaze may collect in the corners.
Sharing in :